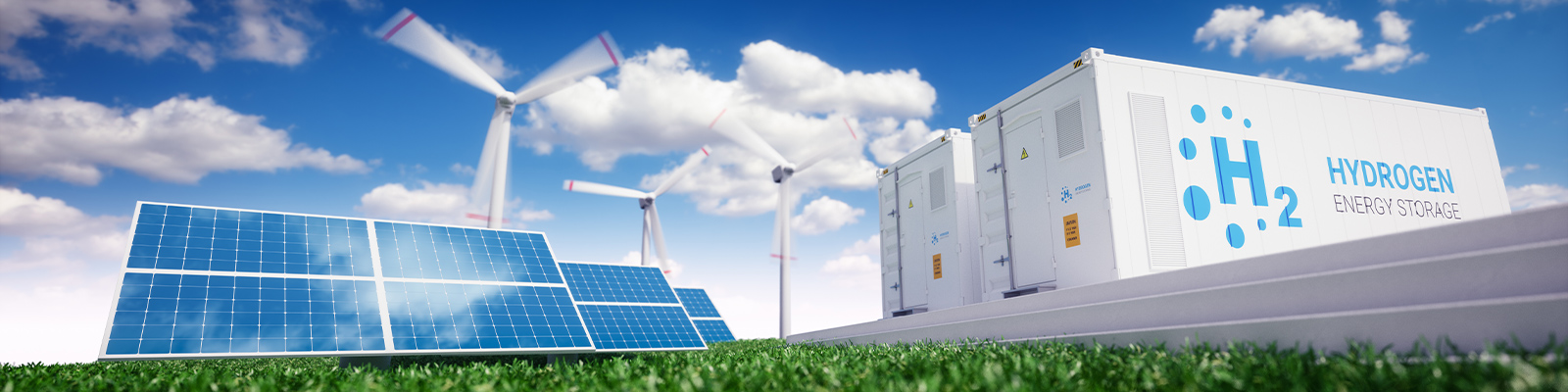
Rely on an experienced and innovative plastic injection molder, such as TechNH, to meet frame requirements
As efforts continue to slow the impact of climate change by substantially reducing the use of fossil fuels, hydrogen has emerged as a source of clean, non-carbon dioxide generating energy. Hydrogen is generated using the process of electrolysis in devices known as electrolyzers. Electrolyzers use electrical energy to separate water into its two components, hydrogen gas and oxygen gas according to the formula: 2H2O ⇆ 2H2+ O2. Renewable energy sources such as solar power or wind power can create the electrical energy to power electrolyzers. Thus, a clean, carbon-free process can manufacture hydrogen, a source of clean energy.
Electrolyzer stacks contain critical internal components known as frames, which are produced through precision plastic injection molding. These frames play a vital role in the overall function of the electrolyzer and require highly accurate molding techniques due to their intricate design. This document provides a concise overview of electrolyzer operation, highlighting the key functions of these frames. It also offers design recommendations to optimize performance and demonstrates how TechNH’s expertise in high-precision, cost-effective manufacturing ensures the production of high-yield electrolyzer frames that meet industry demands.
Overview of electrolyzers
Figure 1 illustrates the basics of electrolyzer operation. Electric current causes input water molecules to oxidize at the anode to produce oxygen gas, protons (H+ ions) and electrons. The protons travel through an electrolyte to the cathode. At the cathode, the protons gain electrons to form hydrogen gas. The physical structure of an electrolyzer consists of stacks of permeable components. Electrolyzers can produce 99.99 % high-purity hydrogen and oxygen gases.
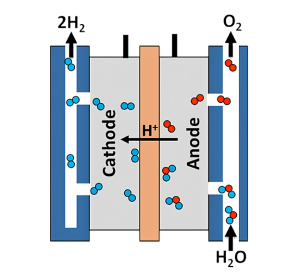
There are several types of electrolyzers, with two main technologies: proton exchange membrane (PEM) and alkaline. Alkaline electrolyzers use a liquid alkaline electrolyte like potassium hydroxide. PEM electrolyzers use a solid polymer electrolyte that allows proton transport. The PEM technology has advantages because it can operate at a high current density and deliver higher energy efficiency due to lower resistive losses. Also, PEM electrolyzers generate higher purity hydrogen gas than can be obtained from alkaline electrolyzers.
Hydrogen, as an energy source, is an excellent energy carrier. It has a higher energy content than the energy content of liquid hydrocarbons such as gasoline and natural gas. Table 1 compares the energy content of hydrogen with two fossil fuels, natural gas and gasoline. The high energy content of hydrogen justifies the use of hydrogen as a suitable replacement for fossil fuels when fuel cells can be a viable power source.
Fuel | Energy Content |
---|---|
Hydrogen | 120.2 MJ/kg |
Natural Gas (95% Methane) | 48.7 MJ/kg |
Gasoline | 43.4 MJ/kg |
Source: Fossil vs. Alternative Fuels – Energy Content
Table 1. Energy content of hydrogen, natural gas and gasoline.
Purpose of PEM electrolyzer frames
The electrolyzer frame is a component that provides support, alignment and containment for the internal parts of the electrolyzer stack. The frame ensures proper operation, safety and efficiency of the electrolyzer. The frame provides the following important functions:
- Structural Support & Alignment – Holds and aligns stack components, maintaining proper compression.
- Sealing & Gas Separation – Prevents leaks and cross-contamination of H₂, O₂, and water.
- Electrical Insulation – Prevents short circuits and ensures proper current flow.
- Fluid & Gas Management – Directs water, hydrogen, and oxygen through the stack.
- Thermal & Chemical Resistance – Withstands high temperatures, pressure, and chemical exposure.
- Manufacturing Efficiency – Designed for precise, high-yield injection molding.
Since PEM electrolyzer frames require precision molding, tight tolerances, and high-performance materials, TechNH’s expertise in complex injection molding is well-suited to manufacturing these components efficiently and cost-effectively.
![]() |
Unhappy with your current molder?See how to seamlessly transfer your tool to get started. |
Get White Paper |
Why use TechNH
TechNH has 20 years of experience in making plastic injection molded electrolyzer frames and is expert in crafting precision-engineered internal frames. The company has extensive expertise in all areas necessary to design and manufacture high-quality frames. These areas include:
- Materials expertise – TechNH engineers have extensive knowledge with high-performance thermoplastics with which they can design and manufacture strong, long-life electrolyzer frames.
- Flexible design expertise – The channels create a torturous path for water to travel through and break down into its component parts, hydrogen and oxygen. Frame shapes can be any size and shape from small circular frames to large rectangular frames.
- Tight tolerance design expertise – TechNH designers have the skills and the equipment to employ tight tolerances to optimize the location and size of design features.
- Cost-effective manufacturing expertise – TechNH can recommend process improvements and mold modifications to optimize the PEM frame injection molding process.
- Quality control expertise – An independent quality department ensures that the client’s PEM frame injection molding process is thoroughly documented and makes repeatable parts to client specifications. Quality engineers use Advanced Product Quality Planning (APQP) to establish PEM frame quality control throughout the appropriate manufacturing process steps. The TechNH Production Part Approval Process (PPAP) prepares the manufacturing team to produce PEM frames that meet and exceed client requirements.
- Metrology expertise – The calibration of equipment in the state-of-the-art metrology lab is traceable to national standards maintained by the National Institute of Standards and Technology (NIST). The highly accurate measurement tools ensure clients receive frames with tight tolerances that meet all their requirements.
In addition, TechNH utilizes principles of sustainability in all its manufacturing processes. The design and manufacturing teams work to minimize material consumption which reduces waste and resource usage. By matching mold concepts and injection molding processes to product designs, TechNH engineers maximize production efficiency.
Extensive experience and expertise enable TechNH to meet the challenging requirements of manufacturing cost-effective, tight tolerance frames. TechNH can meet demanding specifications for electrolyzer frame designs.
Take advantage of TechNH expertise for cost-effective solutions to electrolyzer frame requirements
Internal frames contribute to the proper operation, efficiency and safety of the electrolyzer. It is imperative that the frames be mechanically rigid, precisely aligned with other components of the stack and include adequate cooling channels. TechNH has the knowledge and experience to manufacture internal frames that enhance electrolyzer operation. Contact TechNH at https://www.technh.com/contact/ to cost-effectively produce precision electrolyzer frames that maximize efficiency and performance.