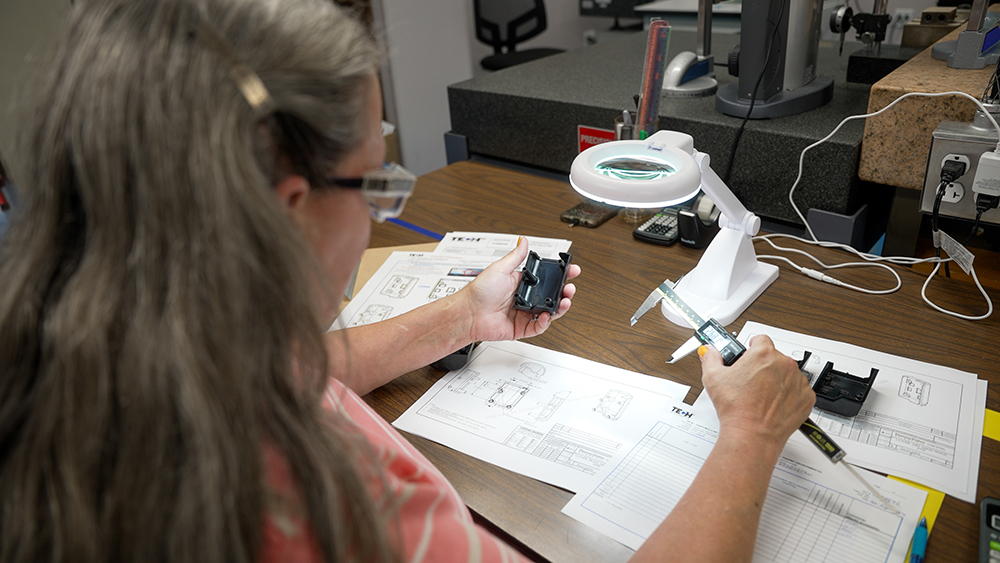
When you contract with TechNH to have a plastic part made, you can use the company’s expertise to define the optimum requirements for your application. TechNH engineers can design your part, develop a customized mold for the part and define the injection molding process. The company also offers secondary services such as testing to ensure compliance with industry standards, sub-assembly tasks, laser marking and packaging. In addition, TechNH’s Regulatory Team, specializing in regulatory standards, can provide guidance on certification and compliance on parts for aerospace, military and medical applications.
Alternatively, a client can supply a complete set of specifications for materials, a mold design, and detailed process requirements developed by their in-house engineering team. If TechNH’s engineering team is confident that they can meet all specifications and requirements, they will manufacture the part.
In either case, TechNH utilizes scientific injection molding principles to minimize waste, avoid product defects, ensure production consistency and maximize yield. Scientific plastic injection molding uses data-driven methods to optimize and control the molding process. The results lead to an enhanced understanding of the molding process for the specific part and improved product quality. TechNH provides feedback on the data generated along with their recommendations.
![]() |
Unhappy with your current molder?See how to seamlessly transfer your tool to get started. |
Get White Paper |
Components of scientific injection molding
The elements of scientific injection molding include material characterization, data collection and analysis, process optimization and mold design and maintenance. Furthermore, scientific injection molding requires well-trained engineers and machine operators to obtain the benefits of the analysis work. The following paragraphs present the primary elements of scientific injection molding and their contribution to improved product quality, higher yield and increased production efficiency.
Injection molding material characterization
It is essential to understand the properties of the material intended for use in the injection molding process. Knowledge of plastic material parameters such as viscosity, flow rates and thermal properties enables proper setup of molding machine parameters, ensuring predictable behavior of the material.
TechNH uses Advanced Product Quality Planning (APQP) to provide a structured approach for planning and executing projects in scientific injection molding. The methodology integrates the design and development phases with the manufacturing process. This includes not only the selection of appropriate materials but also mold design and process optimization. The objective of APQP is to incorporate quality into both the product and process design.
Process analysis
Scientific injection molding requires a thorough analysis of the entire molding process. Engineers analyze the flow of material into the mold. The engineers collect data on process pressure, temperature profiles and material cooling rates. This information provides insights into potential problems with the existing set of process parameters.
TechNH’s engineering team uses Process Failure Mode and Effects Analysis (PFMEA) to identify and mitigate potential risks in the molding process. PFMEA focuses on understanding the interactions between various process parameters and their potential impact on part quality. It involves a detailed analysis of potential failure modes, their causes, and effects, as well as the implementation of controls to minimize these risks. The results from PFMEA can enhance the overall molding process, reduce product dimensional variability and prevent defects.
Data-driven decision making and experiment design
Scientific injection molding relies on data collection and analysis. TechNH’s engineers monitor parameters such as fill time, injection pressure, holding pressure and cooling time during the manufacturing process. They can make adjustments to keep the process within defined limits, ensuring part consistency.
If the process is not performing to expectation, engineering will design experiments to obtain greater insight into the various factors controlling the process and how the resulting output is affected. Studying the effects of parameters such as temperature, pressure and time can lead to the implementation of an optimal mold process.
Validation and control
TechNH uses short prototype runs to evaluate the choice of materials, mold design and molding process parameters. Once the product is in production, the company uses statistical process control tools to ensure that the process operates within defined, and often narrow, limits. If data indicates a process is trending toward a limit, quality control initiates immediate action to investigate and correct the problem.
To manage production quality, TechNH performs testing and validation within the framework of a Production Part Approval Process (PPAP). The company’s PPAP strives to create process stability to produce parts that comply with dimensional, mechanical and cosmetic specifications.
Our goal: Exceed your expectations
TechNH employs the principles of scientific injection molding using Advanced Product Quality Planning, Process Failure Mode and Effects Analysis, and Production Part Approval Process techniques. These programs allow TechNH to optimize material selection and process parameters that can potentially shorten cycle times and reduce costs. Furthermore, these methods reduce defects and waste. The company’s personnel and systems ensure manufactured products are within specification and high quality. TechNH will deliver parts that exceed your expectations.
Ready to talk about your next project? Contact us to get started!