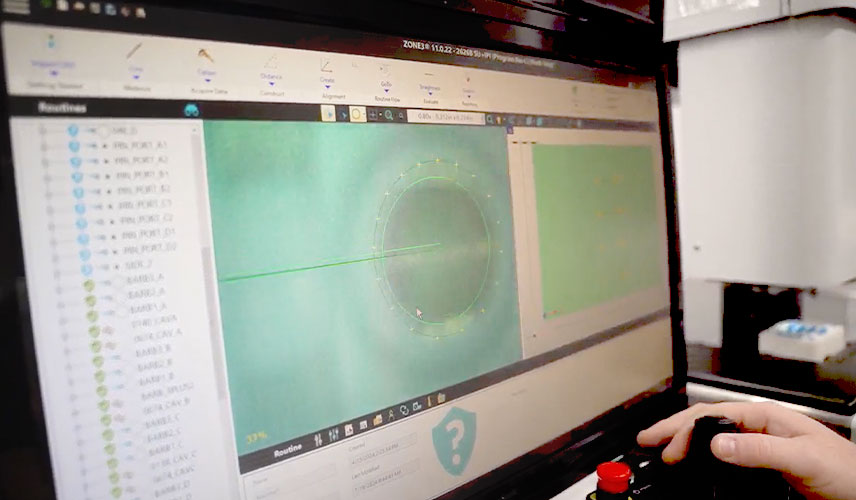
Design for Manufacturability (DFM) is an engineering approach focused on designing products that streamline the manufacturing process, minimize production costs, and maximize efficiency—without sacrificing quality or functionality. This methodology is particularly crucial for producing complex plastic parts with high yields and minimal waste. When applied effectively, DFM can reduce costs by 10% to as much as 50% for plastic injection molded components, especially in industries such as medical devices and alternative energy.
At TechNH, we integrate DFM principles into every stage of custom plastic injection molding to enhance efficiency, reduce cycle times, and optimize overall production costs. In this blog, we’ll explore the core principles of DFM and how they contribute to a more efficient and cost-effective injection molding process.
Understanding Design for Manufacturability (DFM)
DFM is an engineering methodology that guides designers in creating parts optimized for production. It ensures that design elements, such as material choice, part geometry and tolerances, are all aligned with the capabilities of manufacturing processes—leading to easier, faster, and more consistent production. For plastic injection molding, this means considering everything from part wall thickness and material flow to tooling design, draft angles, molding machine control parameters and cooling systems.
While DFM is important across all manufacturing markets, it is particularly pronounced in sectors such as medical, defense, and alternative energy, where part performance and regulatory compliance are crucial. Injection molding without DFM, however, is prone to inefficiencies. Parts might require unnecessary tooling, incur costly rework, or suffer from defects—all leading to higher production costs and delays. Thus, DFM not only streamlines manufacturing but also safeguards quality and compliance.
How DFM Enhances Injection Molding Efficiency
When DFM principles are applied to plastic injection molding, the efficiency gains are notable. Here are the DFM practices that significantly improve injection molding efficiency:
- Close communication with the customer – The mold manufacturer’s engineering team works with the customer’s engineers to understand the application for the part and its most important requirements. Early collaboration with the customer ensures that the mold manufacturer designs the part to achieve the goals for the part and overcome design constraints.
- Optimized material selection – The engineering team works closely with customers to evaluate material selection as a key aspect of Design for Manufacturability (DFM). The chosen thermoplastic or resin must meet essential functional requirements such as strength, flexibility, impact resistance, and chemical durability while also ensuring efficient moldability. Engineers assess factors like flow characteristics, shrinkage rates, and thermal stability to prevent defects and optimize cycle times. Additionally, cost-effectiveness and long-term performance are considered to balance quality with production efficiency. For industries with stringent requirements, such as medical devices and alternative energy, material selection must also comply with regulatory standards, biocompatibility, and environmental resistance to ensure product reliability and safety.
- Optimized mold designs – Mold designers use good design techniques such as ensuring optimal dimensions for strength and uniform wall thicknesses to prevent warping and sink marks. Designers also incorporate tapered walls or draft, ribs and posts to facilitate part removal from the mold. If the customer has an existing mold they are looking to transfer to a new production molding facility, the mold designers can review the design to correct potential problems.
- Use of scientific molding – Software tools, such as CAD and mold flow analysis software, facilitate the development of defect-free mold designs and a repeatable, efficient manufacturing process. Employing scientific molding technology saves development time and costs.
- Minimized waste – Design and production engineers adapt the design to the injection molding process to minimize material waste. Minimizing rework and maximizing resource utilization, reduces waste and allows molders to achieve higher yield rates, which is essential for maintaining cost-efficiency and sustainability.
- Minimized production errors – By addressing potential manufacturing constraints in the design phase, DFM helps mitigate errors, which results in lower defect rates and improved part consistency. This consistency is key in medical and alternative energy applications, where even minor deviations can affect performance and safety.
By identifying and resolving potential production challenges early in development, DFM accelerates project timelines. When parts are developed with DFM, fewer tooling adjustments are required, and cycle times are shortened, allowing faster turnarounds. This translates into cost savings, as fewer resources are spent on troubleshooting or retooling.
![]() |
Minimizing Risk in Medical Device ManufacturingMastering quality and compliance |
Get White Paper |
TechNH’s Unique Approach to DFM
TechNH brings a robust suite of in-house capabilities to the table, making DFM not just a practice but a defining feature of our production approach. We leverage our in-house tooling capabilities to create precise molds that align with DFM principles, optimizing both part quality and production speed. This capability allows for rapid results, enabling us to make swift adjustments based on testing and feedback.
Our in-house regulatory team is another asset that sets TechNH apart. With expertise in regulatory compliance, our team ensures that every part adheres to industry-specific standards, an aspect that’s particularly vital in the medical, and defense markets. Additionally, our cleanroom facilities offer a controlled environment for producing parts, which is essential in sectors requiring sterile and contaminant-free production.
The Competitive Edge: Why Choose TechNH
TechNH’s competitive advantage lies in our holistic approach to DFM, which combines tooling, regulatory oversight and specialized facilities. Our expertise in complex, precision-driven injection molding has made us a trusted partner for clients all over the world. By focusing on quality, compliance, and efficiency, TechNH offers an injection molding solution that few can match.
Our commitment to quality and customer satisfaction drives us to continually refine our processes. We recognize that each client’s needs are unique, and our custom injection molding services are tailored to meet those specifications with the utmost precision.
Partner with TechNH for Superior Injection Molding
Incorporating DFM principles in plastic injection molding delivers measurable benefits: higher production quality, reduced costs, and faster time-to-market. For industries where reliability and performance are non-negotiable, these advantages translate into a significant competitive edge.
At TechNH, we pride ourselves on providing innovative, custom injection molding solutions designed to meet the exacting needs of our clients. Whether you are in the medical, alternative energy, defense, or any other precision-focused sector, our team is here to bring your designs to life with expertise, efficiency and excellence. Contact us to learn how TechNH can enhance your production through DFM-focused, scientific injection molding solutions while saving you both development time as well as design and production costs.