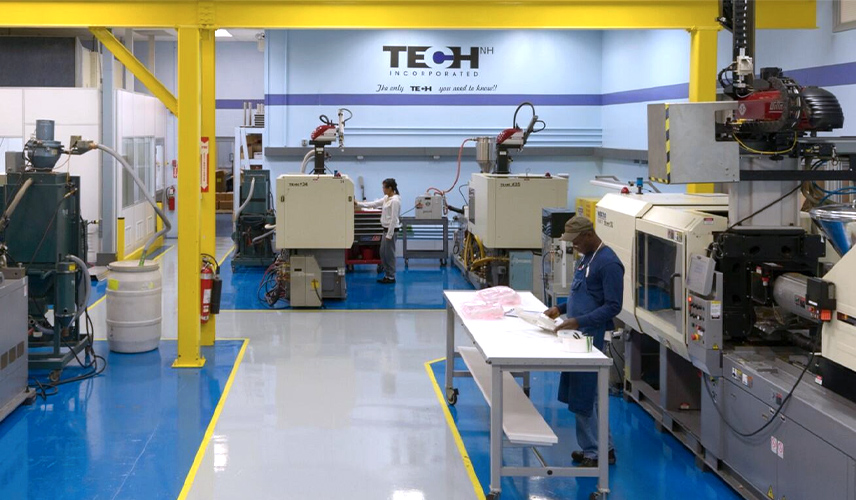
Understanding the technical landscape of the injection molding industry requires familiarity with some specialized terms. Each term carries specific implications for the design, execution, and quality control of manufacturing processes. This article offers a glossary of common terms you’ll encounter within the injection molding industry.
Whether you are a professional in the field or someone keen on understanding the intricacies of manufacturing medical devices and other products, understanding these terms will enhance your ability to engage with experts and ensure your projects meet the highest standards of quality and compliance.
Audit – a systematic, independent examination of a process that is performed at defined intervals and at sufficient frequency to determine if the process activities and results comply with stated requirements and that the process is implemented effectively, and suitable to achieve stated objectives.
AQL (Acceptable Quality Level) – used in conjunction with and established sampling plan to determine the sample inspection quantity for a process. This limit determines the maximum allowable defects by lot quantity size.
cGMP (Current Good Manufacturing Practice) – the practices required in order to conform to the guidelines recommended by agencies that control the authorization and licensing of the manufacture and sale of medical devices. These guidelines provide minimum requirements that a manufacturer must meet to assure that their products are consistently high in quality, from batch to batch, for their intended use.
Clamp Force – The amount of force, measured in tons, exerted by the clamp to hold the two mold halves shut.
Ejector Pins – Also known as ‘push out’ or ‘forged pins’. These are used to push the plastic parts out from the mold.
Extruder – A pump for very thick fluids. The extruder contains a rotating screw that mixes and melts the material and pumps it into the mold.
FAI (First Article Inspection) – is a formal, documented, enumerated process by which parts from a mold are inspected to assure that all critical dimensions meet the specification on the print.
Flash – A molded part defect in which the plastic flows outside the parting line.
IQ (Installation Qualification) – term used for the verification of the correct installation and function of the mold.
Melting Temperature – The temperature at which the plastic pellets melt and become a fluid.
Metrology – the scientific study of measurement.
OQ (Operation Qualification) – is the establishment of the process window and verification standards within which acceptable parts can be manufactured.
PFMEA (Process Failure Mode and Effects Analysis) – an approach to review each step within a process to identify potential failure modes, with the goal of eliminating or mitigating the risks and effects of those failure modes on the process.
PQ (Performance Qualification) – verification of the process using real production conditions.
Scientific (Decoupled) Injection Molding – A systematic approach to molding; it examines the principles behind plastics molding, the behavior of plastics during the molding process and the effect of process variables on part fill, pack and hold portions of the process.
Shot Size – The amount of plastic that is plasticized for each cycle. And the length of the injection strong for each cycle.
Thermoplastics – Polymers that become malleable when heated and then solidify upon cooling.
Tooling or Mold – A mold that produces a desired shape. The tooling can be very simple or very complex as is needed for the part.
Validation – process that verifies the stability of a process to produce an injection molded part.
Verification – evaluates plans, drawings and specifications to ensure the product meets established standards.
Contact us today to discuss your project requirements and discover how our expertise and capabilities can bring your vision to life. With TechNH as your partner, you can expect exceptional quality, precision, and reliability every step of the way.